Selecting the right pneumatic tubing material is critical in ensuring the efficiency, longevity, and safety of any pneumatic system. Pneumatic systems rely on compressed air to transmit and control energy, and the tubing material plays a substantial role in maintaining pressure and preventing air leaks. One key factor in choosing the best material is understanding its implications on system performance, cost, and suitability for specific applications.
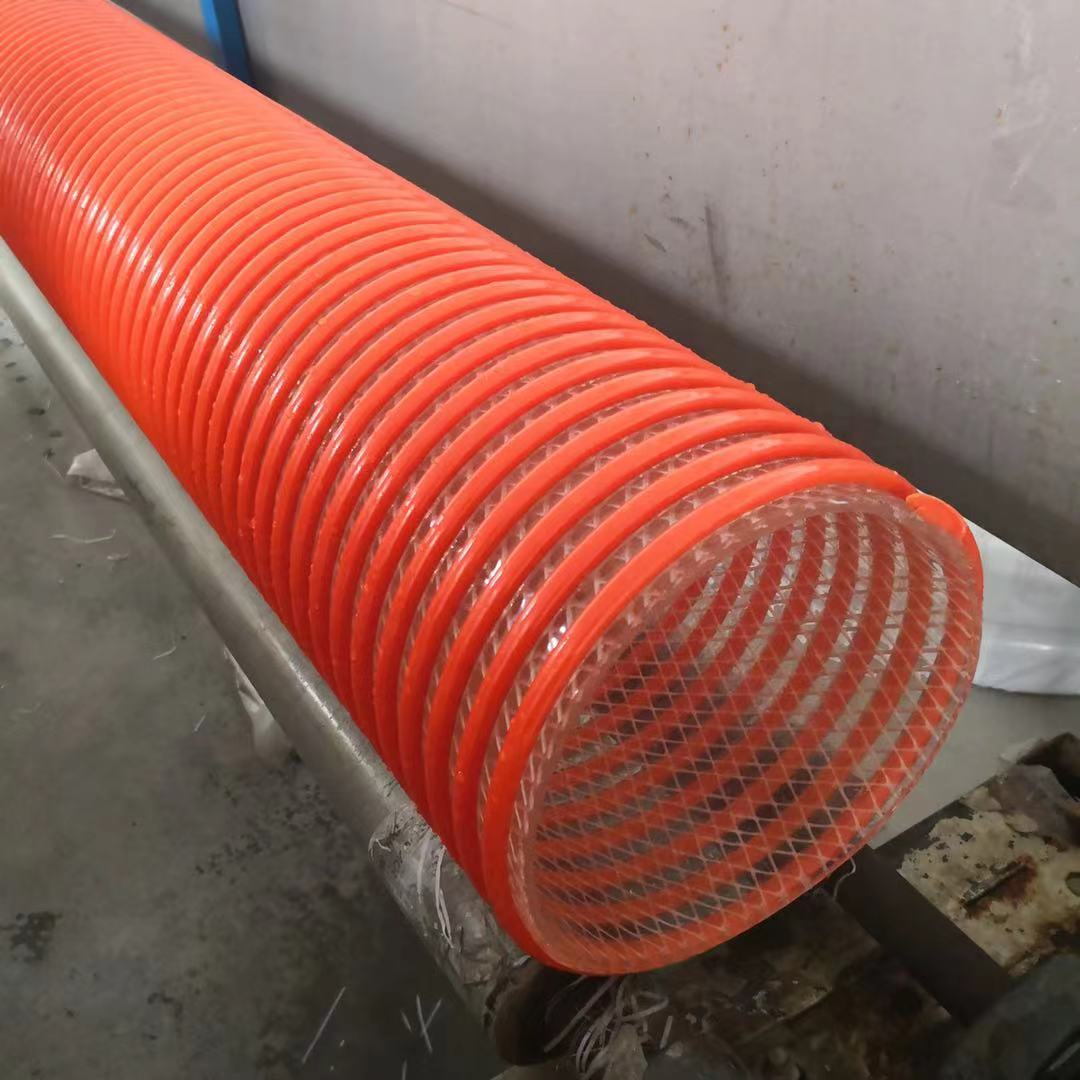
Polyurethane has emerged as a popular option due to its flexibility and resistance to kinking and abrasion. Its elasticity allows it to bend easily, making it ideal for dynamic applications where the tubing undergoes constant motion. Polyurethane’s durability means reduced maintenance costs, making it a trustworthy choice in manufacturing settings where uptime is crucial.
For high-temperature environments, PTFE (Polytetrafluoroethylene) tubing stands out. Known for its excellent thermal stability, PTFE can withstand extreme temperatures while maintaining its integrity, making it perfect for applications involving high heat. Its non-reactive nature also makes it suitable for chemical transportation, adding to its versatility in various industries.
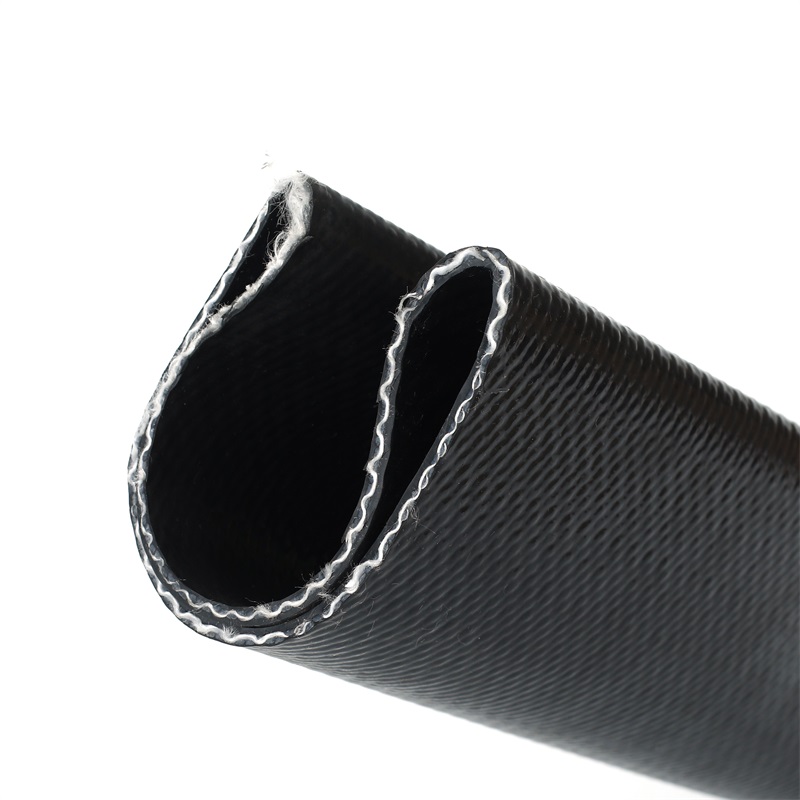
If cost-effectiveness is a primary concern, consider using polyethylene tubing. Although it has lower temperature and pressure thresholds compared to other materials, polyethylene is remarkably lightweight and easy to install. Its affordability doesn't compromise on reliability, especially in lower-stress environments like home and light industrial applications. It offers reliable performance without significant impact on the budget, proving that quality doesn't always have to come with a hefty price tag.
pneumatic tubing material
In environments where chemical resistance is vital, nylon tubing offers a robust solution. Nylon’s inherent toughness and ability to resist many chemicals make it suitable for demanding chemical applications. However, it is essential to note that nylon can be susceptible to moisture absorption, potentially affecting its dimensional stability. Thus, it's crucial to assess the specific environmental conditions before selecting nylon as a solution.
When strength and toughness are critical, consider stainless steel tubing. While it incurs higher initial costs, its unmatched durability and corrosion resistance in harsh environments can save substantial repair and replacement costs in the long term. Stainless steel is often preferred in applications where system failure could have severe consequences, like in the aerospace and automotive industries.
Consulting with experts in pneumatic systems can provide insights tailored to your specific needs. Analyzing the operational environment, desired lifespan, and maintenance capabilities will ensure that the selected tubing material offers optimal performance without compromising safety or efficiency. Keeping abreast of emerging materials and technology is also advisable, as innovations continue to offer new possibilities for improving pneumatic systems.
Real-world experience and expert advice underscore the importance of making informed decisions when selecting pneumatic tubing materials. By considering factors such as material properties, economic implications, and specific application requirements, you ensure not only the efficiency of the pneumatic system but also its safety and reliability.