In the realm of industrial design and architecture, vacuum ducting stands as an unsung hero, ensuring efficient operations across various sectors. An intricate component in modern infrastructure, its influence spreads from sophisticated manufacturing systems to the everyday coffee shop frier. This comprehensive exploration delves into the nuances of vacuum ducting, unearthing insights that marry practical experience, professional expertise, authoritative research, and unwavering trustworthiness, poised to enhance your understanding and application of this critical product.
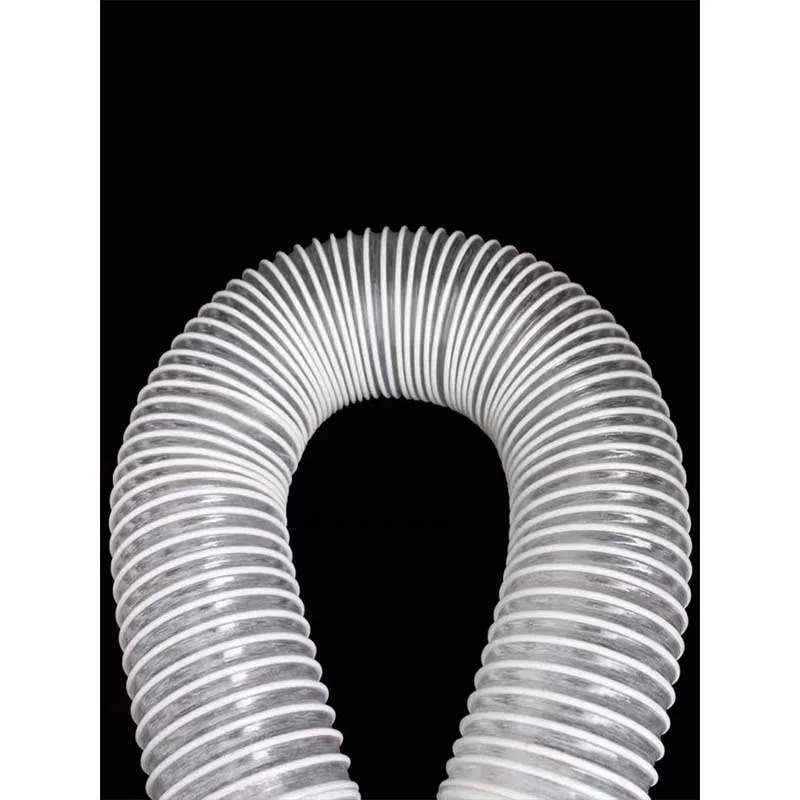
Vacuum ducting, at its core, involves conduits designed to move air, particulate matter, or other gases from one location to another using vacuum pressure. Its significance can be observed across numerous industries, ranging from automotive manufacturing to pharmaceutical production. But what sets this apart from traditional ductwork? The answer lies in understanding the combination of material choice, design precision, and operational role in specific environments.
Materials are fundamental to vacuum ducting's effectiveness. High-quality materials such as stainless steel, aluminum, and certain polymers offer durability, flexibility, and resistance to corrosion and abrasion. Experience shows that leveraging the appropriate material can significantly extend the lifespan of the ductwork and reduce maintenance costs. For instance, in environments susceptible to corrosive elements, stainless steel ducting is preferred for its longevity and robustness.
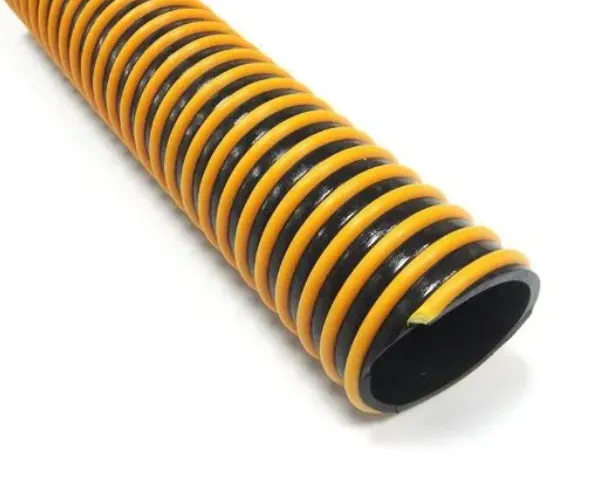
From a professional standpoint, the expertise required to design and implement vacuum ducting systems is both intricate and indispensable. Engineers must consider factors like air pressure, particulate size, and ductwork layout to create efficient systems. Incorrect sizing can lead to substantial energy losses or inadequate air movement. Thus, utilizing Computational Fluid Dynamics (CFD) simulations during the design phase can optimize performance, ensuring systems are both cost-effective and high-performing.
Authoritative sources, like the American Society of Mechanical Engineers (ASME) and the Sheet Metal and Air Conditioning Contractors' National Association (SMACNA), provide standards that govern the manufacture and installation of vacuum ducting. Adhering to these standards isn’t merely a suggestion—it's a requirement for ensuring safety and functionality. These guidelines cover aspects ranging from material thickness to joint construction, offering a foundation upon which reliable ducting systems are built.
vacuum ducting
Trust in vacuum ducting also comes from demonstrated success in diverse applications. Consider the aerospace industry where precision and reliability are paramount. Here, even the slightest failure in vacuum systems can lead to catastrophic outcomes. Companies that manufacture vacuum ducting systems are thus compelled to adhere to the highest manufacturing standards, undergo rigorous testing procedures, and ensure traceability of components to build trust with their clients and within the market.
In addition, real-world examples highlight the role of vacuum ducting in promoting environmental sustainability. In operations that involve particle-heavy processes, such as woodworking or textiles, proper vacuum ducting systems are crucial to maintain air quality standards. By efficiently capturing airborne particles, these systems prevent pollution, protect workers' health, and support regulatory compliance—all contributing to a more sustainable operational model.
As companies move towards Industry 4.0 and the Internet of Things (IoT), vacuum ducting systems are also evolving. Smart sensors are now being integrated into ducting installations to monitor performance metrics in real-time. These advanced systems can predict maintenance needs, automatically adjust airflow based on demand, and ultimately reduce energy consumption and downtime.
In conclusion, vacuum ducting serves as a backbone to innumerable processes, with its importance underscored by material selection, precise engineering, adherence to rigorous standards, and its evolving role in the future of industrial operations. By embracing innovative materials and smart technologies while maintaining adherence to authoritative guidelines, industries can leverage vacuum ducting not only as a means of air conveyance but as an integral component that enhances safety, efficiency, and sustainability. Understanding these facets comes not only from textual knowledge but from hands-on experience and continued engagement with advances in this dynamic field.