Choosing the right oxy acetylene hose size is crucial for ensuring optimal performance and safety in welding and cutting applications. The hose plays a vital role in transporting gases from the source to the torch, and its size can affect the efficiency and safety of your operations. Understanding the different sizes available and how they impact your work is essential for anyone involved in metalworking industries.
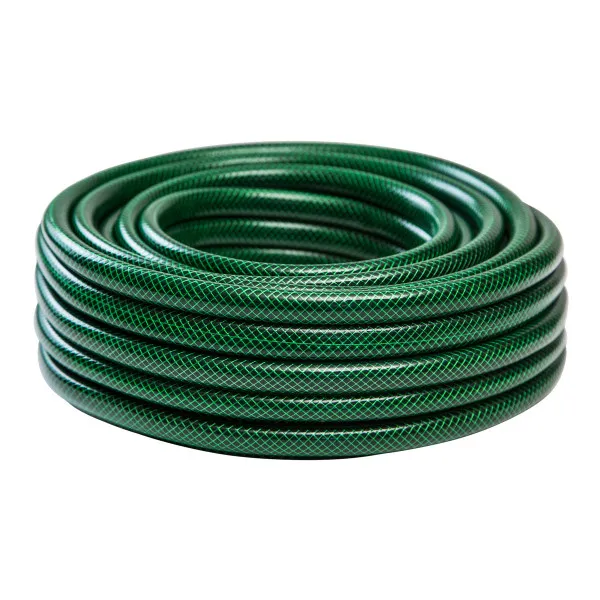
Oxy acetylene hoses come in various sizes, typically measured by their internal diameter. The most common sizes are 3/16 inch, 1/4 inch, and 3/8 inch. Each size has specific applications and benefits, making it important to select the correct one based on your particular needs.
The 3/16 inch hose is often used for light-duty applications and is ideal for intricate welding tasks that require precision and control. Its smaller diameter means it is lightweight and flexible, which can reduce operator fatigue during prolonged use. However, due to its limited capacity, it may not be suitable for high-volume gas flow tasks, as this can strain the hose and reduce its lifespan.
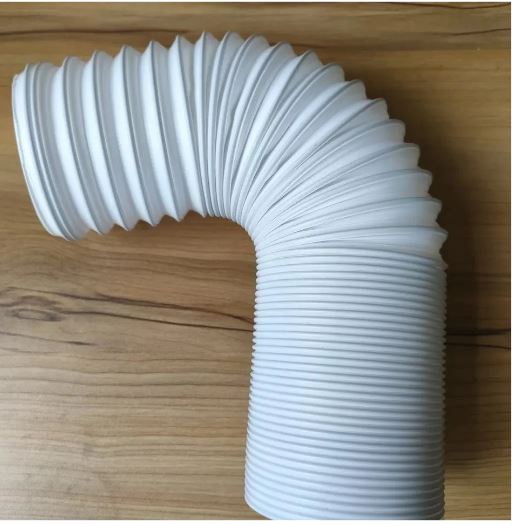
For medium-duty applications, the 1/4 inch hose is often preferred. It strikes a balance between flexibility and capacity, making it versatile for various welding and cutting tasks. This size is suitable for both hobbyists and professionals, providing enough gas flow for moderate work without the bulkiness of larger hoses. The 1/4 inch hose is a popular choice for its ability to handle a wide range of oxy acetylene setups without compromising on efficiency or safety.
The 3/8 inch hose is designed for heavy-duty applications, where high gas flow is required. Its larger diameter allows for rapid gas delivery, making it the preferred choice for industrial settings and demanding environments. Although it is less flexible than smaller hoses, its robustness and capacity to handle high pressures make it indispensable for tasks involving thick metals and prolonged periods of operation.
oxy acetylene hose sizes
When selecting an oxy acetylene hose, it's also important to consider the material and construction. Hoses are generally made from rubber, neoprene, or a blend of both. Rubber hoses are flexible and resistant to wear and tear, while neoprene hoses offer enhanced durability and resistance to oils and flames. Choosing the right material based on your environment can extend the life of your hose and improve safety.
Additionally, fittings and couplings are critical components that should not be overlooked. Ensure that the hose and torch connectors are compatible to prevent leaks and ensure a secure connection. Regular inspection and maintenance of hoses and fittings are imperative to detect wear and damage, which can compromise safety and performance. A well-maintained hose not only enhances performance but also prevents potential hazards such as gas leaks or flashbacks, which can be dangerous.
Furthermore, understanding the compatibility of hoses with various auxiliary equipment is crucial. Different hoses might be better suited for specific attachments, regulators, and torches. Proper training and adhering to safety standards can significantly mitigate risks associated with oxy acetylene equipment.
Safety should always be your primary concern when working with oxy acetylene setups. Using the correct hose size and ensuring that it is in good condition are fundamental steps in creating a safe working environment. Adequate ventilation, protective gear, and adherence to safety protocols must accompany the proper selection and use of equipment. Training and regular safety checks can help prevent accidents and ensure a safe and productive workspace.
In conclusion, knowing the different types of oxy acetylene hose sizes and their specific applications can greatly impact the efficiency and safety of your welding and cutting operations. By choosing the appropriate size and type of hose, conducting regular maintenance, and following safety standards, you can enhance your productivity while minimizing risks. Whether you are a skilled professional or a novice in the field, attention to these important details will support better outcomes in your work with oxy acetylene equipment.