Understanding the Essentials of Oxy Acetylene Hoses An Expert's Perspective
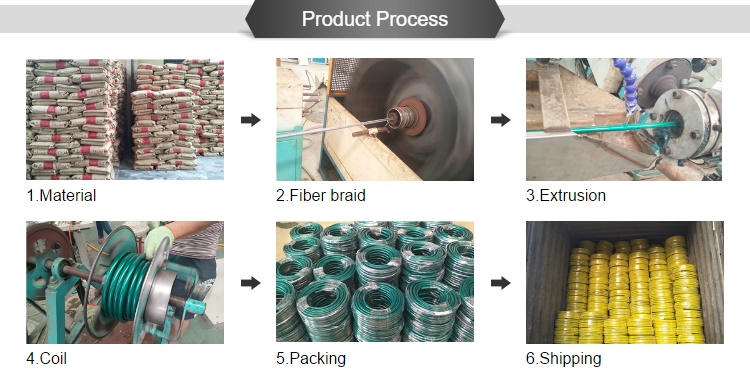
In the realm of welding and metal cutting, the right equipment can make a significant difference in the quality and safety of the work performed. A crucial component of this equipment is the oxy-acetylene hose, which plays a pivotal role in directing the gases safely and efficiently from the tanks to the torch. As an expert in welding materials and safety, I will walk you through the fundamental aspects of oxy-acetylene hoses, offering insights that will enable both novices and seasoned professionals to make well-informed decisions.
At its core, an oxy-acetylene hose serves as the conduit for oxygen and acetylene gases, which are combined to produce a flame capable of melting metals. This hose often comes in a dual-hose configuration, color-coded to differentiate between oxygen (generally green) and acetylene (usually red). This color distinction is critical for preventing potential mishaps, as the wrong connection can lead to dangerous outcomes.
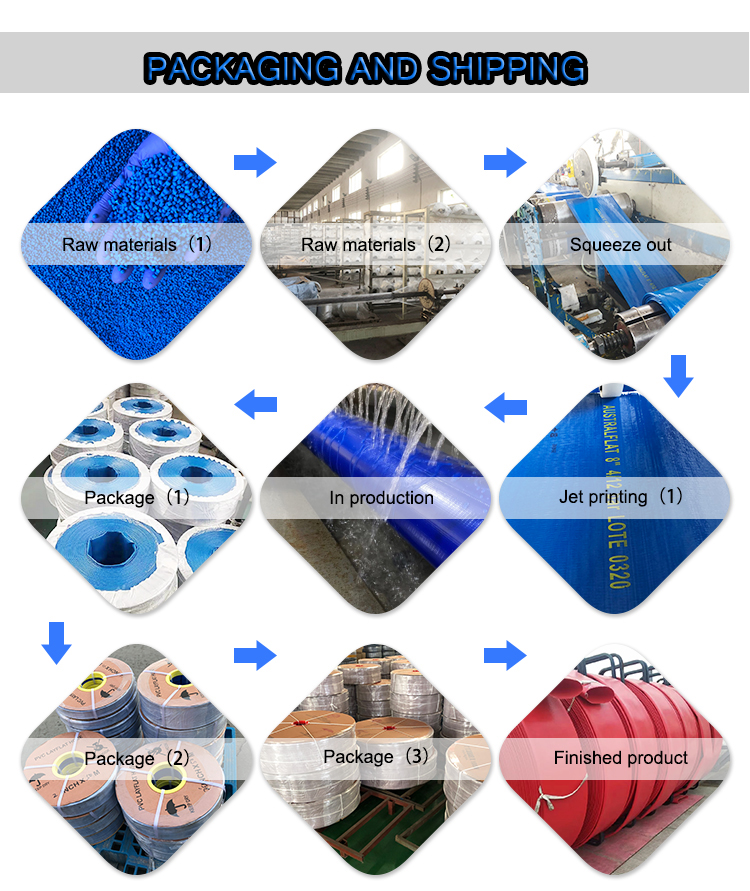
When selecting an oxy-acetylene hose, it is essential to consider the materials used in its construction. Hoses are typically made from synthetic rubber, neoprene, or other flexible materials that can withstand high pressures and varying environmental conditions. The synthesis of these materials ensures durability, flexibility, and resistance to adverse conditions, which is essential for maintaining consistent performance over time.
One of the primary concerns with oxy-acetylene hoses is their susceptibility to wear and tear, which can lead to leaks. Leaks not only compromise the quality of the work but also pose significant safety hazards. Regular inspection is recommended to ensure that the hoses do not have cracks, loose fittings, or signs of deterioration. Implementing a routine check can help catch these potential issues early, ensuring a safe working environment.
oxy acetylene hose
In addition to routine inspections, proper storage and handling of the hoses can significantly prolong their life span. Make sure that hoses are stored away from direct sunlight or areas with extreme temperatures. Avoid coiling the hoses too tightly, as sharp bends can cause internal damage, reducing their effectiveness and safety.
Another crucial aspect to consider is compatibility. Not all hoses are suited for every type of welding and cutting application. Ensuring that the hose is compatible with the specific equipment and gases it will be used with is imperative. Compatibility checks can prevent malfunction and ensure that your welding tasks are executed efficiently and safely.
Furthermore, training and adherence to safety protocols are indispensable when working with oxy-acetylene hoses. Training should cover not only operational aspects but also emergency response actions—identifying gas leaks, understanding torch operation, and knowing the routine for extinguishing accidental workplace fires. Safety data sheets and operating manuals should be readily accessible, emphasizing the importance of informed usage.
Innovation in the welding industry continues to evolve, leading to advances in the technology and materials used for oxy-acetylene hoses. Modern hoses often come with added layers for enhanced durability and reinforced fittings to prevent accidental disconnections. Staying abreast of these advancements and updating equipment accordingly can lead to improved safety and productivity.
In conclusion, an oxy-acetylene hose is more than just a conduit for combustible gases—it is a critical component that ensures the safety and efficiency of welding and cutting operations. By investing in high-quality hoses, adhering to routine maintenance, and fostering a culture of safety through training and protocol adherence, users can optimize their equipment's performance and protect themselves from potential hazards. Whether you're new to the field or an experienced professional, understanding the intricacies of oxy-acetylene hoses is pivotal to mastering the art and science of welding and cutting metal.