When navigating the seemingly endless world of welding equipment, selecting the right tools is imperative for safety and efficiency. Among essential components, the twin welding hose stands out as a vital instrument in any welder's arsenal. With decades of development and innovation driving forward its efficiency and safety features, it's critical to understand the intricacies of this indispensable piece of equipment.
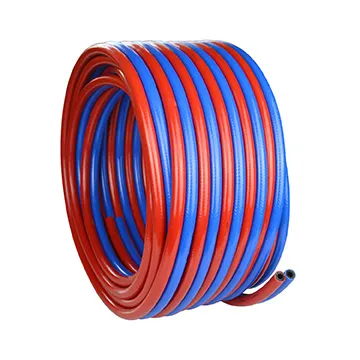
The twin welding hose is uniquely designed to handle two types of gas simultaneously, typically oxygen and acetylene. This duality is crucial for oxy-fuel welding and cutting processes, making the hose an indispensable component in various industrial applications. The welding process relies heavily on precise gas flow to produce the correct flame needed for welding, cutting, or brazing, which exemplifies the hose's vital role in maintaining high-quality work.
Firstly, experience with twin welding hoses often highlights the importance of choosing products from reputable manufacturers. High-quality hoses are constructed to withstand pressures varying between 200 to 300 PSI and temperatures ranging from -20°F to 150°F, ensuring durability under frequent use. When sourced from renowned brands, these hoses are made from synthetic rubber with excellent abrasion resistance, minimizing the risk of wear and tear even in the harshest working environments.
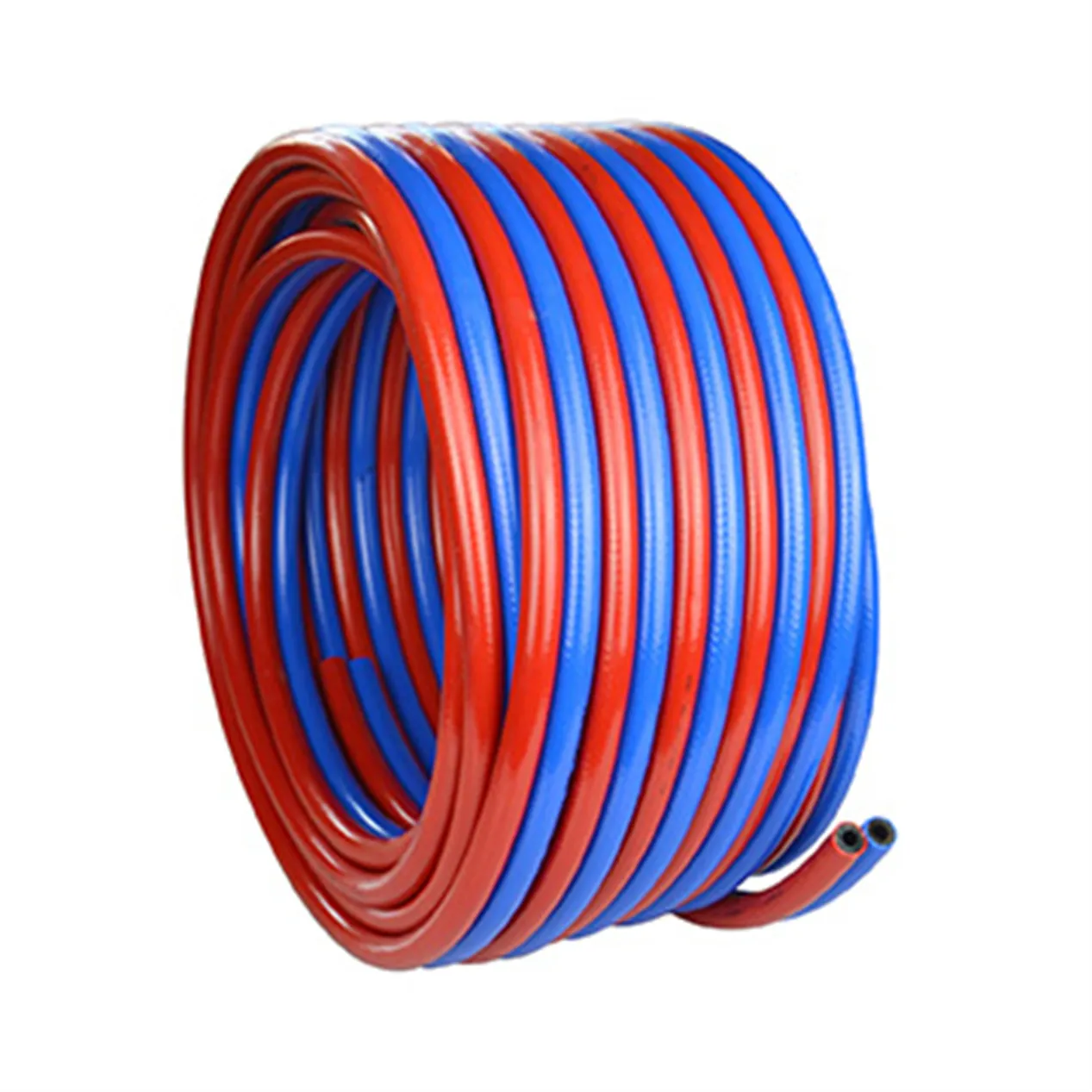
An expert’s choice of twin welding hoses will generally be driven by a few pivotal factors, including hose diameter, length, and material quality.
The diameter of the hose affects the flow rate of gases – a critical consideration in tasks involving precision welding where constant pressure is essential. Likewise, the length must balance flexibility and reach while avoiding unnecessary bulk that could potentially cause hazards or inefficiencies in workspace navigation.
twin welding hose
The material integrity of the twin hose is another area that showcases expertise and meticulous engineering. Manufacturers frequently use high-quality synthetic rubber to ensure flexibility, kink resistance, and durability. Additionally, investing in hoses with a robust inner lining prevents permeation of gases, which safeguards the integrity of the internal gas flow crucial for precise flame control.
Authoritative discussions often highlight the compliance of twin welding hoses with industry standards, such as the Compressed Gas Association (CGA) or the Occupational Safety and Health Administration (OSHA) regulations. Compliance ensures that hoses undergo rigorous testing and quality control processes, offering peace of mind to users who rely on these tools for critical operations. The knowledge that these hoses have passed stringent safety tests enhances their reliability and overall authoritative standing in the market.
Trustworthiness in twin welding hoses is primarily demonstrated through their reliability in maintaining consistent gas delivery and their role in sustaining safety in potentially hazardous environments. A trustworthy hose will not degrade quickly over time, not only preventing leaks but also extending the lifespan of the welding equipment connected to it. This long-term trust is built upon a foundation of user testimonials and proven track records in various industrial settings.
Overall, the twin welding hose is an essential yet often undervalued player in welding and cutting processes. When chosen wisely, it drastically enhances the efficiency and safety of operations, reflecting its underlying value in the welding community. As technology progresses and newer models emerge, they bring with them advanced materials that further ensure safety, reliability, and precision – qualities that resonate at the heart of all professional and authoritative discourse surrounding this essential component.