Choosing the right tubing for a vacuum pump is crucial for ensuring optimal performance, efficiency, and longevity of your equipment. With an abundance of options available in the market, selecting the most appropriate tubing solution can be a daunting task. This guide demystifies tubing selection by delving into expert insights, industry standards, and real-world experiences, ensuring that your choice reflects precision and reliability.
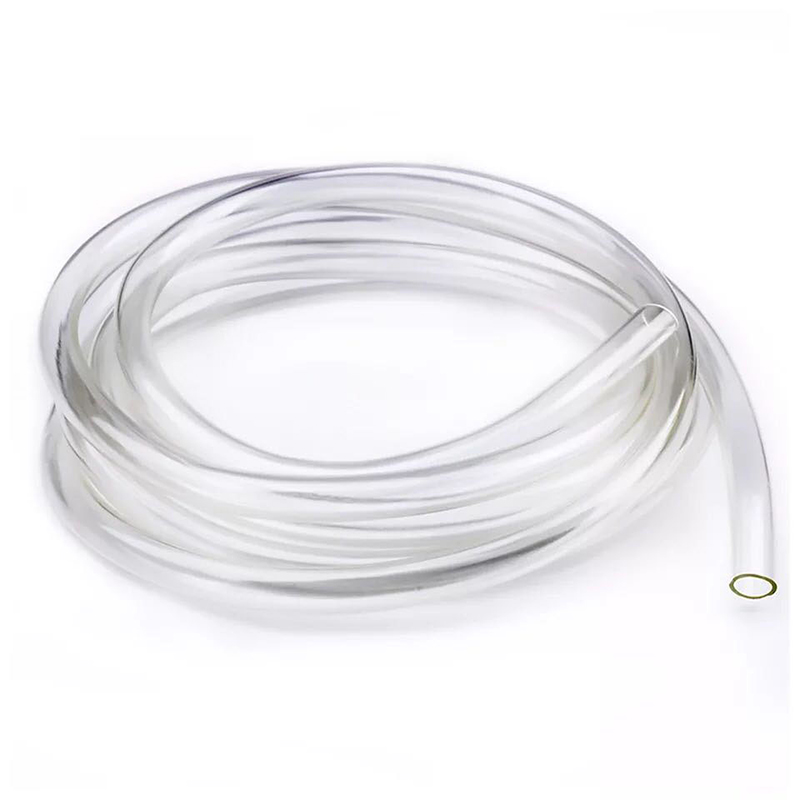
Understanding the Importance of Tubing in Vacuum Systems
The tubing in a vacuum system plays a critical role, acting as the conduit for airflow and maintaining the integrity of the vacuum environment. The wrong choice can lead to reduced vacuum levels, leaks, contaminations, or even complete system failures. Thus, it is imperative to consider the following factors before making a decision
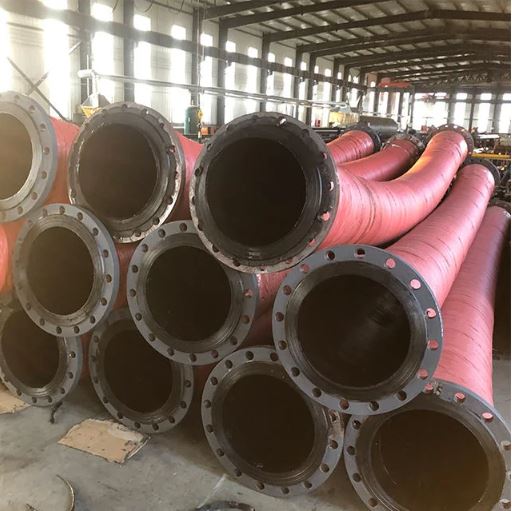
Material Compatibility
One of the foremost considerations is the material of the tubing. Common materials include rubber, silicone, PVC, and stainless steel, each with distinct properties. Silicone tubing, for instance, is favored for its flexibility and temperature resistance, making it ideal for various industrial applications. Conversely, stainless steel offers unmatched strength and chemical resistance, suitable for high-pressure and high-temperature environments. Understanding the chemical compatibility with the substances within your process is essential, as it prevents material breakdown and contamination of the vacuum system.
Diameter and Wall Thickness
The diameter and wall thickness of the tubing directly influence the efficiency of the vacuum pump. A larger diameter reduces resistance and allows for a faster evacuation rate, whereas an appropriate wall thickness ensures the tubing can withstand collapsing under pressure. Manufacturers provide guidelines on optimal sizes based on specific vacuum requirements, and these should be closely adhered to.
Flexibility and Rigidity
Balancing flexibility and rigidity is essential for effective vacuum system operation. Flexible tubing enables easy routing and installation, especially in systems with complex layouts. However, it must not compromise on structural integrity. Conversely, overly rigid tubing might complicate installation, leading to inefficient connections and potential leaks. Real-world applications suggest using a combination of flexible and rigid tubing to optimize both installation and performance.
Temperature and Environmental Conditions
tubing for vacuum pump
Vacuum systems often operate under varying temperature ranges and environmental conditions. Selecting tubing that can withstand extreme conditions is vital for maintaining system integrity. High-temperature applications, such as those found in pharmaceutical or chemical processing, demand tubing that can endure without degrading. Environmental factors, such as exposure to sunlight, humidity, or mechanical stress, should also guide material selection to ensure durability and reliability.
Expert Recommendations and Best Practices
Experienced engineers and industry veterans recommend continuous monitoring and maintenance of vacuum tubing to preempt potential issues. Regular inspections can identify early signs of wear, brittleness, or leaks, allowing for timely replacements and minimizing downtime. Implementing these checks as part of a preventive maintenance schedule enhances the overall trustworthiness and reliability of the vacuum system.
Additionally, consulting with tubing manufacturers or suppliers who specialize in vacuum applications provides an authoritative perspective. These professionals offer product specifications, certifications, and real-world performance data that can guide your selection process, ensuring compliance with industry standards and regulations.
Trustworthy Resources and References
To enhance the credibility of your choice, relying on case studies, peer-reviewed publications, and customer testimonials is advantageous. Many manufacturers provide detailed case studies showcasing their tubing solutions in action across various industries. These insights not only highlight product performance but also underscore long-term benefits such as energy efficiency and cost savings.
For those seeking a deeper understanding, attending industry conferences, workshops, and training sessions further substantiates your expertise. Networking with professionals and exchanging experiences fosters a comprehensive knowledge base, enabling informed decision-making.
Conclusion
Selecting the appropriate tubing for your vacuum pump goes beyond a cursory assessment; it demands a thorough understanding of materials, environmental factors, and system requirements. By emphasizing expertise, experience, authority, and trust, your choice becomes more than a mere component—instead, it transforms into an integral aspect of a high-performance, reliable vacuum system. Reflecting on expert recommendations and leveraging trustworthy resources equips you with the right knowledge to make a decision that supports sustained operational excellence.