Selecting the right tubing for vacuum pump systems is critical for maintaining operational efficiency and ensuring optimal performance in diverse industrial applications. Vacuum pumps are integral to various processes, from chemical processing to semiconductor manufacturing, and the right tubing can significantly impact their functionality.
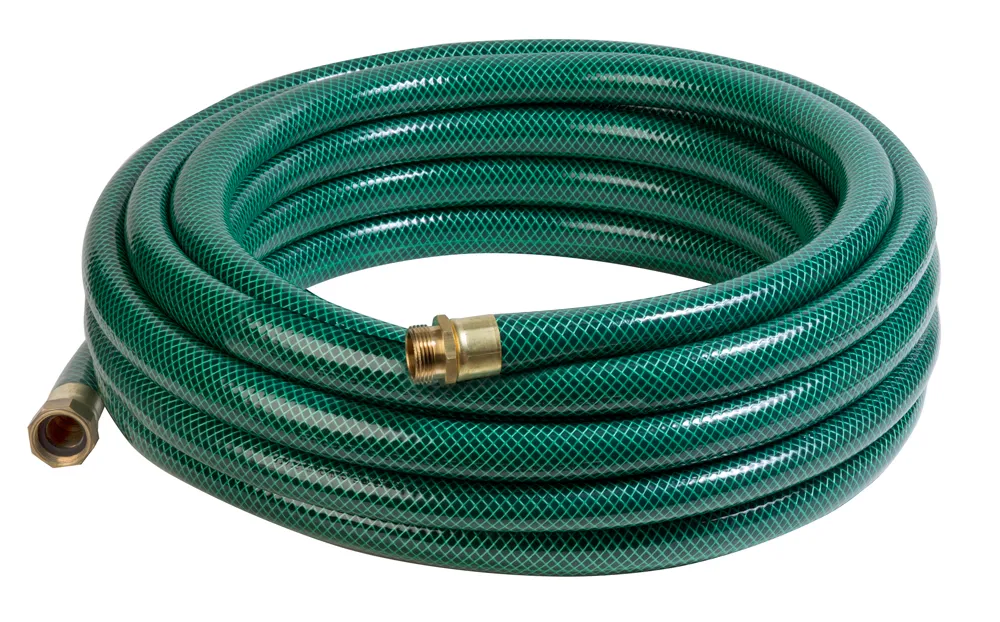
The first step in choosing suitable tubing is understanding the specific requirements of the vacuum system in question. This involves considering factors such as the chemical compatibility, temperature tolerance, and mechanical strength of the tubing material. These parameters are crucial because they determine how well the tubing will perform under designated conditions.
Chemical compatibility is paramount in environments where the vacuum pump must handle reactive or corrosive gases. Tubing made from materials like PTFE (Polytetrafluoroethylene) or stainless steel is often recommended due to their exceptional resistance to a wide range of chemicals. PTFE, being non-reactive, allows it to be used safely with aggressive substances without fear of degradation, ensuring longevity and reliability.
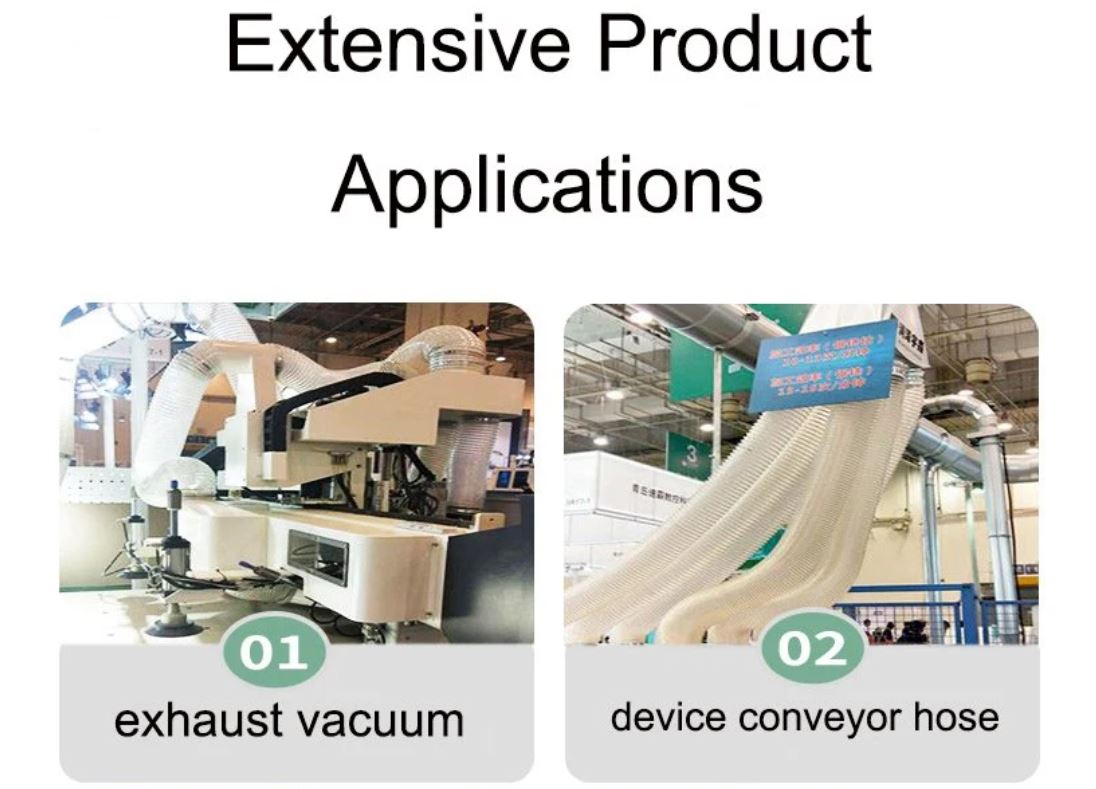
Temperature tolerance of tubing material is another critical consideration. Industrial applications often demand that systems operate under extreme temperatures, both high and low. Silicone tubing, for instance, is known for its flexibility and resilience, capable of maintaining integrity across a broad temperature range. Conversely, PVC tubing, although cost-effective and easy to install, may not withstand higher temperatures as effectively as silicone or rubber alternatives.
Mechanical strength and durability also play a significant role in the selection process.
Tubing must withstand the vacuum pressures without collapsing. Reinforced rubber tubing, for example, offers excellent abrasion resistance and structural integrity, making it ideal for high-pressure applications and environments where external wear-and-tear is a concern.
tubing for vacuum pump
Beyond material considerations, the dimensional specifications of the tubing, such as diameter and wall thickness, must align with the vacuum pump’s operational parameters. Tight connection between different components prevents leakages, maintaining the vacuum’s integrity and avoiding costly disruptions in the process flow. Flexible tubing is often preferred for its ease of installation and ability to accommodate equipment layout changes without compromising the vacuum seal.
Another crucial aspect is energy efficiency, as choosing the right tubing can contribute to reduced energy consumption. Properly sized tubing minimizes pressure drops, allowing the vacuum pump to operate more efficiently. This not only lowers energy bills but also enhances the operational lifespan of the pump, providing a return on investment that benefits long-term sustainability goals.
When considering the setup, it is essential to assess the environmental impact as well. Options like hydrogenated nitrile, which combines the benefits of synthetic and natural rubber, provide a more sustainable solution. Choosing eco-friendly materials supports environmental stewardship and complies with increasingly stringent regulations regarding emissions and waste handling.
From an expertise and authority perspective, consulting with specialists in vacuum technology can offer invaluable insights. Engineers and technicians with practical experience can provide detailed recommendations tailored to the specific processes and equipment, ensuring seamless integration and superior performance. Trustworthy suppliers often provide comprehensive guidance and documentation, including compatibility charts and technical support, assisting in informed decision-making.
In conclusion, selecting the proper tubing for vacuum pumps involves a nuanced understanding of material properties and system requirements. Prioritizing chemical compatibility, temperature tolerance, mechanical strength, and energy efficiency is essential. Moreover, leveraging expert advice enhances the overall trustworthiness of the implementation, facilitating safe and efficient industrial operations. This strategic approach not only improves immediate performance outcomes but also positions the system for enduring success in a competitive marketplace.