Reinforced vacuum tubing plays a crucial role in various industries, ranging from automotive to medical applications, ensuring reliability and efficiency in systems where vacuum transfer is paramount. This advanced tubing is specifically designed to withstand high pressure and resist collapse, making it a staple in settings where both performance and safety are highly prioritized.
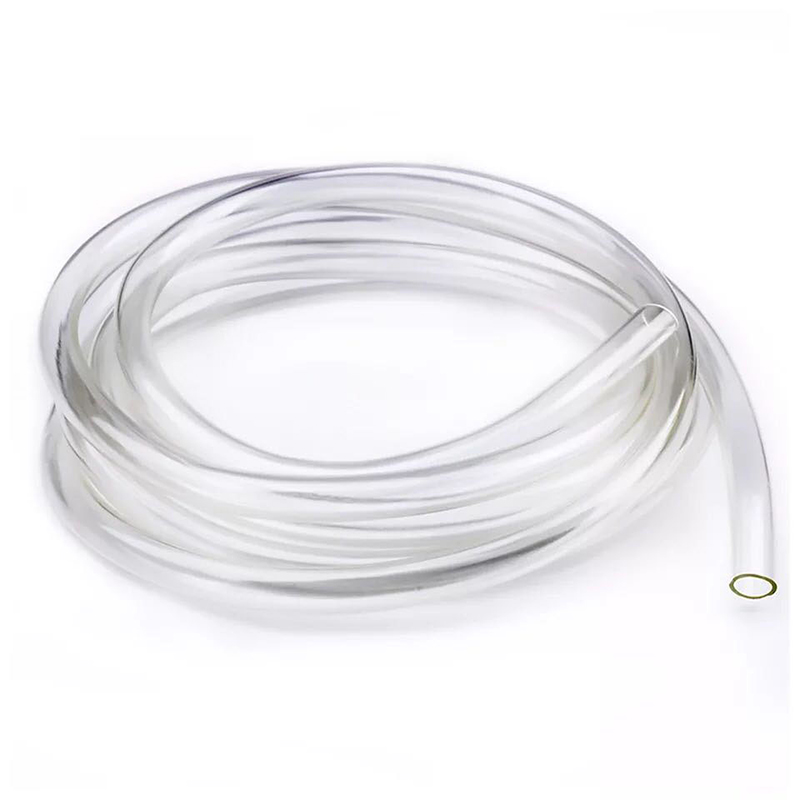
When selecting reinforced vacuum tubing, the material composition is a key factor to consider. Typically made from high-grade plastics, rubbers, or a combination of both, these materials are engineered to offer excellent resistance to wear, abrasion, and chemical interactions. For instance, silicone-reinforced tubing is a popular choice in the medical industry due to its high-temperature resistance and inert properties, which ensure that there is no reaction with transported substances.
In automotive industries,
reinforced vacuum tubes are central to the functioning of engines and emission control systems. They maintain optimal engine performance by efficiently transferring vacuum without any pressure loss. Reinforced with braided polyester or stainless steel wire, these tubes are capable of handling the rigorous demands of high-pressure environments under the hood. Mechanics often stress the importance of using only high-quality reinforced tubing to prevent engine malfunction and maintain vehicle efficiency.
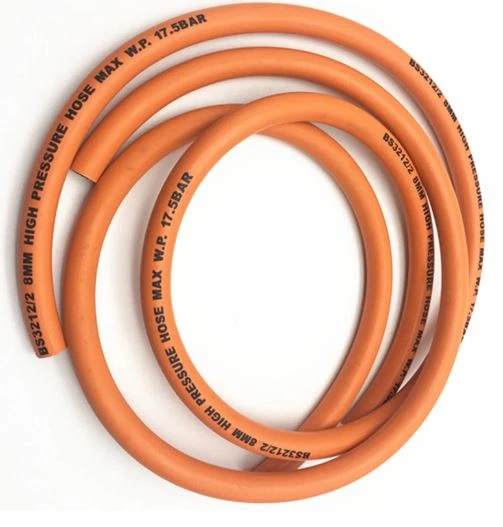
Moreover, in industrial environments, where vacuum systems are often large and complex, reinforced vacuum tubing ensures the seamless operation of machinery by providing stable and reliable vacuum transfer. The durability of reinforced tubing reduces maintenance costs and downtime, as it rarely needs replacement compared to non-reinforced alternatives. For this reason, many engineers and facility managers insist on reinforced tubing, as it significantly enhances the longevity and performance of industrial equipment.
Environmental factors such as UV radiation, ozone, and extreme temperatures can also impact the performance of vacuum tubing. Reinforced vacuum options often include additives and coatings that enhance their resilience to these external conditions. This characteristic makes them ideal for outdoor applications and ensures that they maintain their integrity over prolonged exposure to harsh environments.
reinforced vacuum tubing
The expertise involved in manufacturing reinforced vacuum tubing cannot be overstated. Leading manufacturers employ state-of-the-art technology to ensure precision in each tube's diameter, wall thickness, and reinforcement density. This meticulous attention to detail guarantees consistency and reliability in performance, fostering trust among users who rely on these products for critical applications. It’s this level of expertise that distinguishes top-tier reinforced vacuum tubing from standard products in the market.
Trustworthiness is further cemented by rigorous testing and certification processes. Certifications from recognized bodies like ISO or ASTM are testament to the reinforced vacuum tubing’s quality and performance. Customers should always verify these certifications as part of their selection process to ensure they are investing in a product that meets the highest standards of safety and efficacy.
Documented real-world experiences further establish the credibility and effectiveness of reinforced vacuum tubing. Case studies from various sectors demonstrate its versatile applications and reliability. For example, an engineering firm significantly improved the safety and efficiency of their HVAC systems by switching to braided reinforced vacuum tubing, leading to a reduction in maintenance incidents and an increase in energy efficiency. Similarly, a biopharmaceutical company noted a marked improvement in the sterility and accuracy of its fluid transport systems after integrating reinforced vacuum tubing.
In conclusion, reinforced vacuum tubing is indispensable across multiple industries due to its robustness, reliability, and adaptability. The careful selection based on material composition, manufacturing precision, and environmental resilience can dramatically impact the efficiency and safety of vacuum systems. For industry professionals seeking to improve or maintain their system's integrity, investing in high-quality reinforced vacuum tubing is a decision backed by both experience and expertise. For business leaders, these considerations not only contribute to operational excellence but also align with broader goals of sustainability and long-term cost-effectiveness.