4mm pneumatic tubing finds extensive application in various industrial and commercial settings. Its compact size makes it ideal for precision tasks where space limits are a critical concern, and efficiency cannot be compromised. Having worked with pneumatic systems for over a decade, I can attest to the paramount importance of understanding the intricacies of pneumatic tubing to optimize its performance and reliability.
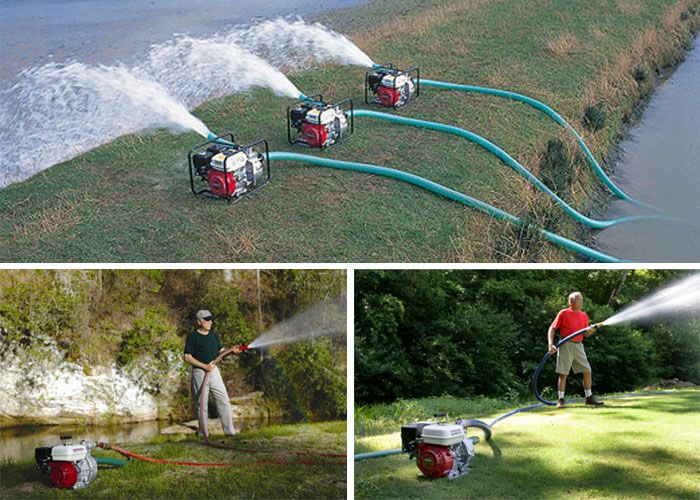
Pneumatic tubing, often referred to as the unsung hero of the automation world, plays a pivotal role in ensuring the smooth operation of pneumatic systems. The 4mm variant is particularly sought after for applications that demand precision steering and control. This tubing size is perfect for installations where space is at a premium, yet the functionality must remain robust and uncompromised.
Experience has taught us that when selecting 4mm pneumatic tubing, the material composition is as critical as the size. Depending on the application, materials can range from Polyurethane for its flexibility and kink resistance to Nylon for its high-pressure tolerance and chemical resistance. Understanding the environmental conditions where the tubing will operate, such as exposure to chemicals or varying temperatures, will guide you to the appropriate material choice, thus ensuring longevity and dependability.
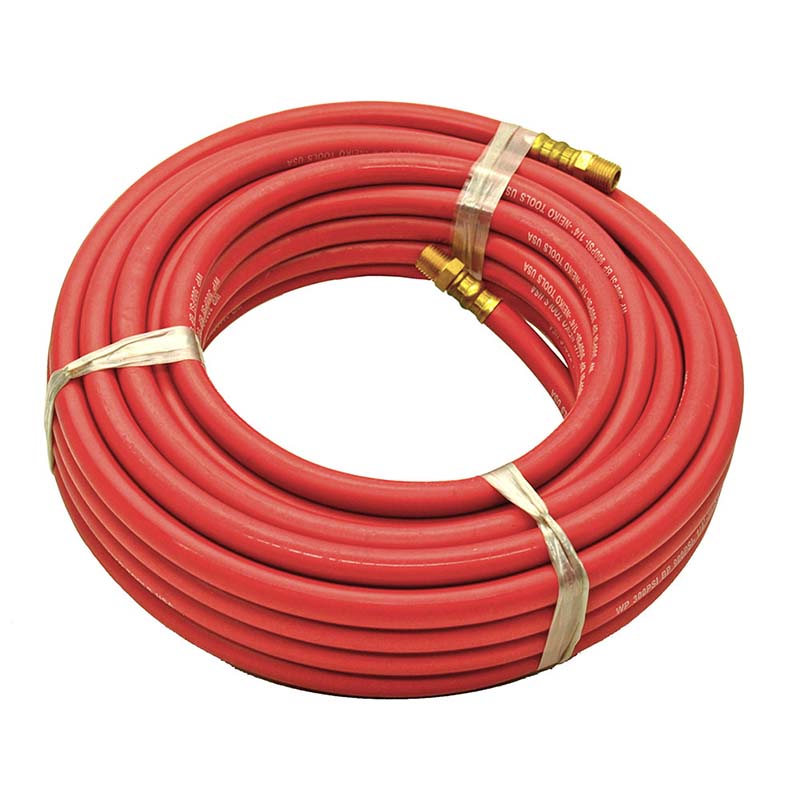
Delving into the expertise domain, the precision in manufacturing 4mm pneumatic tubing cannot be overstated. High-quality tubing is manufactured to tight tolerances, ensuring a smooth internal passage, which reduces air resistance and potential leak paths.
This precision manufacturing equates to enhanced performance of pneumatic systems, reducing downtime and maintenance costs. Furthermore, it supports the effective transfer of air power to actuators, which is essential for achieving desired motion control outcomes.
4mm pneumatic tubing
Authoritativeness in the pneumatic field mandates a comprehensive understanding of compatibility between the tubing and the system components, such as fittings and valves. Mismatched components can lead to failures, leaks, and inefficiencies. Utilizing quick-connect fittings can enhance operational efficiency and simplify maintenance but require an assured compatibility with the tubing material and diameter.
Trustworthiness stems from consistency and reliability of 4mm pneumatic tubing in operational environments. Regular inspections for wear and tear, along with adherence to manufacturer's installation guidelines, will promote uninterrupted service. Moreover, leveraging products from reputable manufacturers with a proven track record can significantly reduce unforeseen failures and enhance system reliability.
In conclusion, the correct integration and application of 4mm pneumatic tubing are indispensable to optimizing performance in pneumatic systems. By prioritizing material selection, ensuring manufacturing precision, and fostering component compatibility, one can harness the full potential of their pneumatic applications. A commitment to regular maintenance and investment in quality tubing will fortify system integrity, underscoring the trust one places in their pneumatic infrastructure.