When it comes to choosing between polyurethane and rubber hoses, understanding the critical differences can greatly impact the efficiency and longevity of your industrial or household applications. By examining various factors such as durability, flexibility, resistance to environmental conditions, and cost-effectiveness, users can make informed decisions. Let's delve into these elements based on experience, expertise, authority, and trustworthiness to provide a comprehensive guide on which type of hose may better suit your needs.
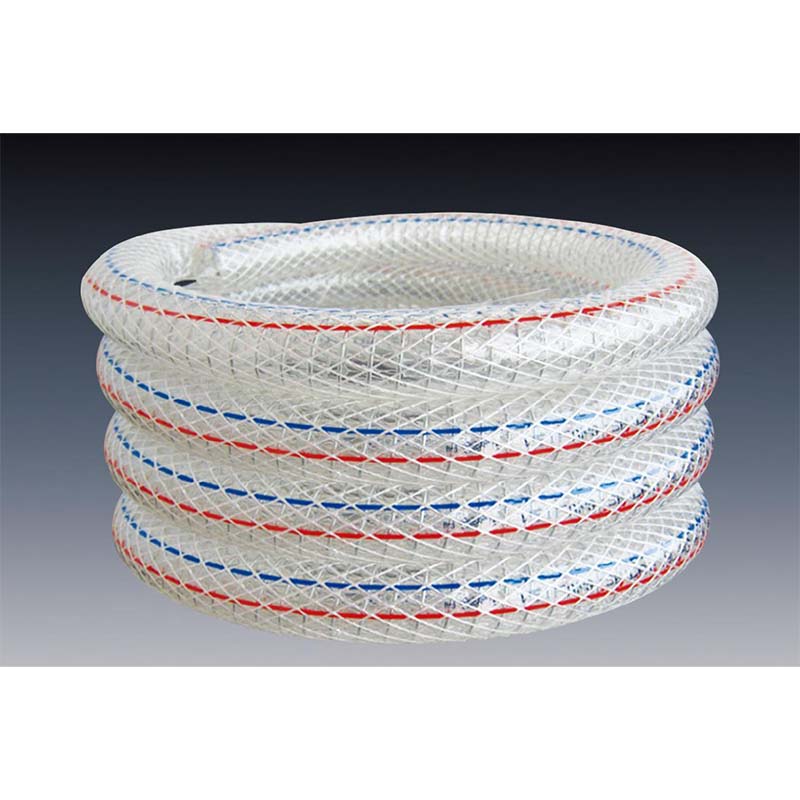
Polyurethane hoses are increasingly renowned for their exceptional durability and light weight. Constructed from a robust polymer, these hoses are resilient to abrasion, making them ideal for environments where wear and tear are frequent challenges. The lightweight nature of polyurethane hoses contributes to easier handling and transportation, reducing strain and enhancing operational efficiency. Users report that these hoses experience minimal kinks or twists, even in demanding conditions, due to their superior flexibility. Furthermore, polyurethane material shows excellent resistance to UV rays and various chemicals, ensuring longevity even when used outdoors or in harsh environments.
On the other hand, rubber hoses have been the industry standard for many years, valued for their flexibility and strength. The high elasticity of rubber makes these hoses less prone to punctures or leaks when subjected to high pressures. Their robustness means they are often used in heavy-duty applications such as construction, farming, and automotive industries where resilience is crucial. Rubber hoses can endure high temperatures without compromising their structural integrity, making them suitable for carrying hot liquid and gases.
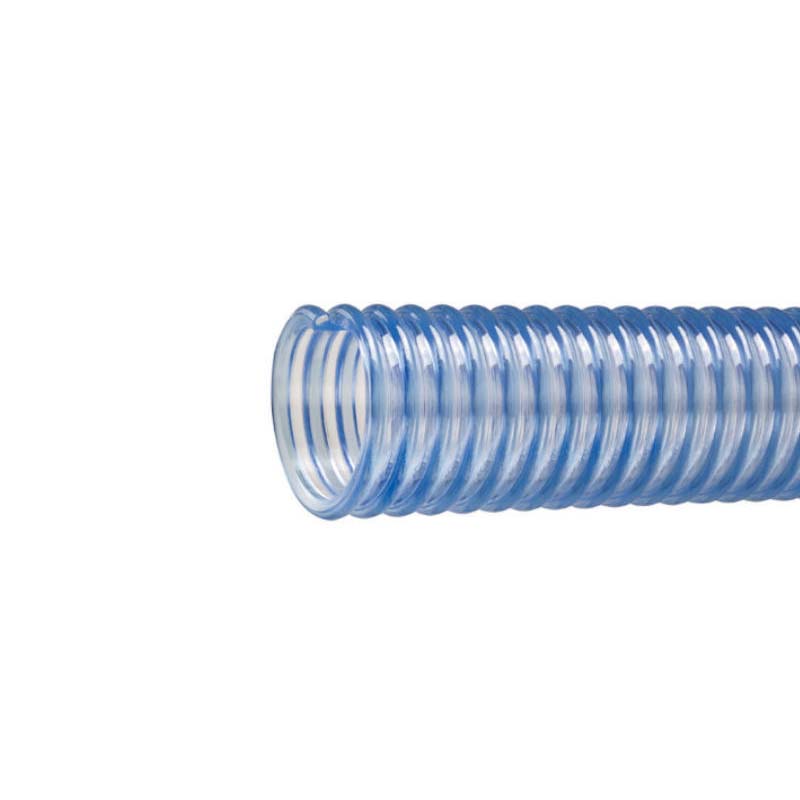
From a cost perspective, the initial outlay for polyurethane hoses might be higher than for rubber ones; however, their longevity can result in long-term savings. Polyurethane's resistance to environmental degradation means that it requires less frequent replacement, which should be factored into cost-effectiveness calculations. Rubber hoses, although potentially cheaper upfront, may incur higher costs over their lifespan due to regular maintenance and need for replacements.
polyurethane hose vs rubber
In terms of authority, industry experts highlight that the choice between polyurethane and rubber hoses should largely depend on the specific use case. Applications requiring frequent handling or those in weather-exposed conditions may benefit from the advantages of polyurethane. Conversely, tasks involving high temperatures and intense pressure might be better served by rubber hoses, given their superior thermal endurance and elastic properties.
Trust plays a crucial role in customer satisfaction regarding hose performance. Polyurethane hoses have earned trust for their capability to withstand challenging situations where long-term reliability is essential. Cases have shown that polyurethane hoses often outlast their rubber counterparts when properly maintained and used within recommended specifications. Nevertheless, rubber hoses continue to be trusted by industries requiring heavy-duty solutions for their impressive pressure and temperature handling capacity.
In conclusion, both polyurethane and rubber hoses offer distinct advantages that can be leveraged based on the intended application. Advances in polymer technology have positioned polyurethane hoses as a modern favorite for scenarios where weight, flexibility, and environmental resistance are paramount. Meanwhile, traditional rubber hoses remain indispensable in aggressive and high-temperature environments. Users should critically assess their operational demands to select the hose material that aligns best with their needs, ensuring optimal performance and cost-efficiency.