In the realm of industrial machinery and automation, the choice of pneumatic tubing material can significantly influence the efficiency, durability, and safety of a pneumatic system. With numerous options available on the market, selecting the right tubing material can be a daunting task; however, understanding the strengths and weaknesses of each option can facilitate a more informed decision. This article delves into the critical aspects of choosing pneumatic tubing by examining material properties, application environments, and cost considerations.
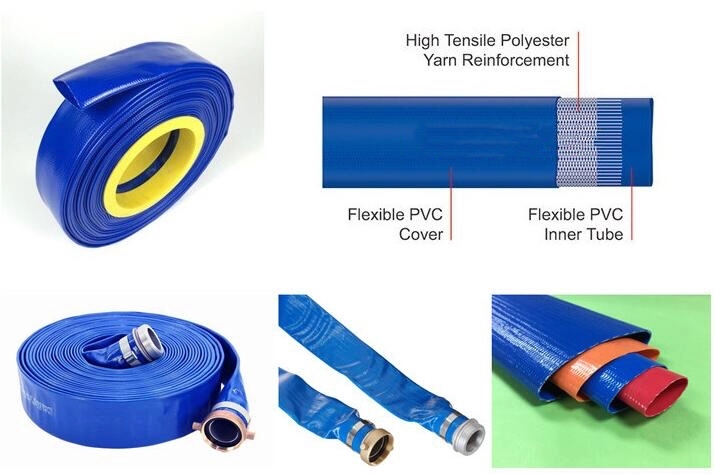
Pneumatic tubing serves as the lifeline of pneumatic systems, transporting compressed air to actuate components. The primary materials used in these systems include polyurethane, nylon, polyethylene, and PVC. Each material offers distinct advantages and limitations, which warrants a careful evaluation against the specific demands of the intended application.
Polyurethane stands out due to its exceptional flexibility and kink resistance. It is particularly useful in applications that involve complex routing or where the tubing may be frequently moved and repositioned. Furthermore, polyurethane is resistant to abrasion and can withstand a broad range of temperatures, making it ideal for dynamic environments. However, its susceptibility to certain chemicals and UV radiation may limit its use in outdoor or chemically harsh environments.
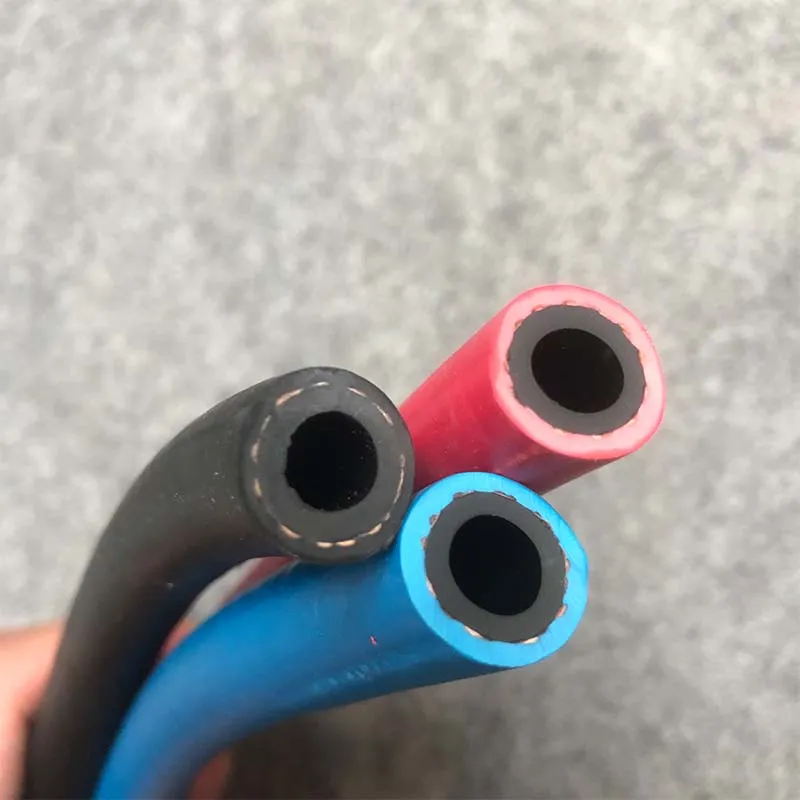
Nylon, renowned for its high strength-to-weight ratio, offers excellent resistance to chemicals, abrasion, and heat. This makes it suitable for high-pressure applications that require robust performance under challenging conditions. Nylon's rigidity, however, can be a drawback in applications that demand high flexibility. Its moisture absorption property might also alter certain mechanical characteristics, which should be considered in humid environments.
Polyethylene tubing is commonly used for its cost-effectiveness and ease of installation. It provides satisfactory chemical resistance and is typically employed in low-pressure applications. Nevertheless, polyethylene has a lower temperature range and may not be the best choice for environments with extreme conditions or where high pressure is a factor.
PVC tubing is valued for its versatility and affordability. It offers good chemical resistance and can be used in diverse applications from food and beverage to medical sectors. While PVC is less flexible than polyurethane, its rigidity can be advantageous in static installations. Its performance, however, declines with exposure to high temperatures or UV radiation, and it may not be suitable for pressure-critical applications.
pneumatic tubing material
Selecting the appropriate pneumatic tubing material involves a comprehensive understanding of each material's properties in relation to the application requirements. The operating pressure, temperature range, chemical exposure, and environmental conditions must be meticulously assessed. Additionally, compliance with industry standards and regulations is essential to ensure the safety and reliability of the tubing system.
Cost considerations also play a pivotal role in material selection. While initial material costs are important, one must also consider installation expenses, maintenance needs, and the potential cost implications of operational downtimes or system failures. Balancing upfront costs with long-term performance and reliability will yield a more economical and efficient pneumatic system.
Gleaning insights from industry experience and expert recommendations can greatly enhance decision-making in tubing material selection. Consulting with manufacturers and suppliers who possess extensive knowledge of material properties and system requirements is invaluable. Trials or pilot runs may also offer practical insights into material performance under actual operating conditions, reducing the risk of unforeseen compatibility issues.
Trust in well-documented case studies and credible sources can reinforce the confidence in material choices. Established manufacturers and industry leaders often publish valuable resources, outlining their research findings and case analyses that can aid in informed decision-making.
In conclusion, the selection of pneumatic tubing material hinges on a careful assessment of material properties, application requirements, and cost-effectiveness. Understanding the unique advantages and constraints of each material option will equip you with the expertise necessary to design a robust and efficient pneumatic system. Emphasizing trust of professional insights, adhering to industry standards, and balancing cost-effectiveness are key strategies in achieving an optimal pneumatics setup.