Mastering the art of oxy-acetylene welding can be a game-changer for both hobbyists and professionals in the welding industry. Understanding the intricacies of this age-old method begins with choosing the right equipment, and a key component is the oxy-acetylene welding hose. This article dives deep into the essential knowledge required to make informed decisions about this crucial element, enhancing your welding setup in terms of performance and safety.
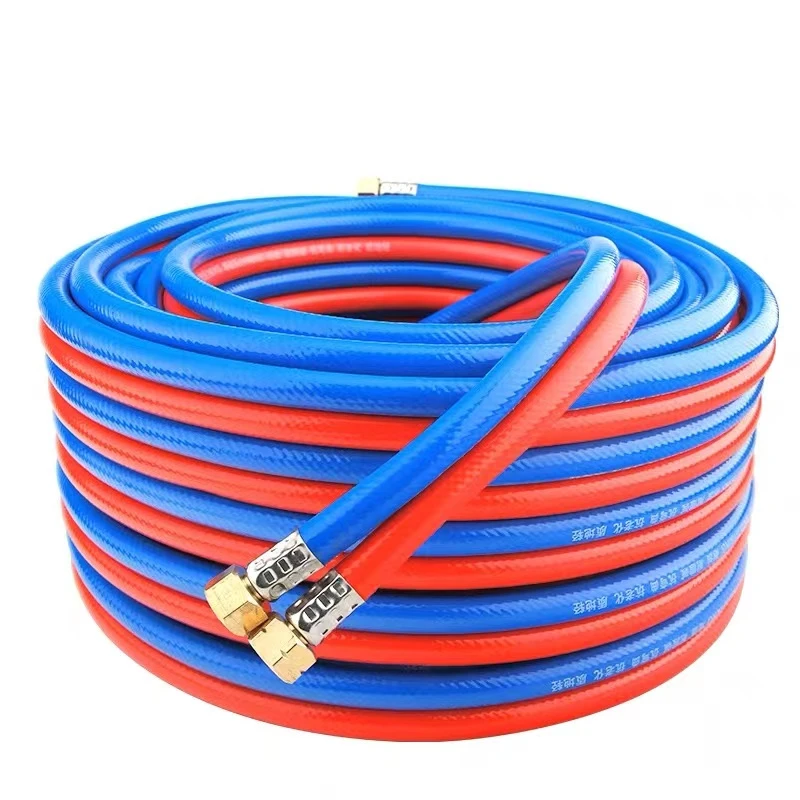
When it comes to oxy-acetylene welding, the hose acts as the lifeline of the process, channeling the acetylene and oxygen gases safely and efficiently. The quality and specifications of the hose can significantly influence the overall welding experience. One must consider several technical aspects, such as material composition, diameter, length, pressure capacity, and compatibility with welding torches.
The material of the hose is paramount. Typically, these hoses are manufactured from durable synthetic rubber or high-grade thermoplastics, designed to withstand high pressures and prevent gas leaks. A high-quality hose will be resistant to abrasion, kinking, and weather conditions, assuring durability and reduced maintenance costs.
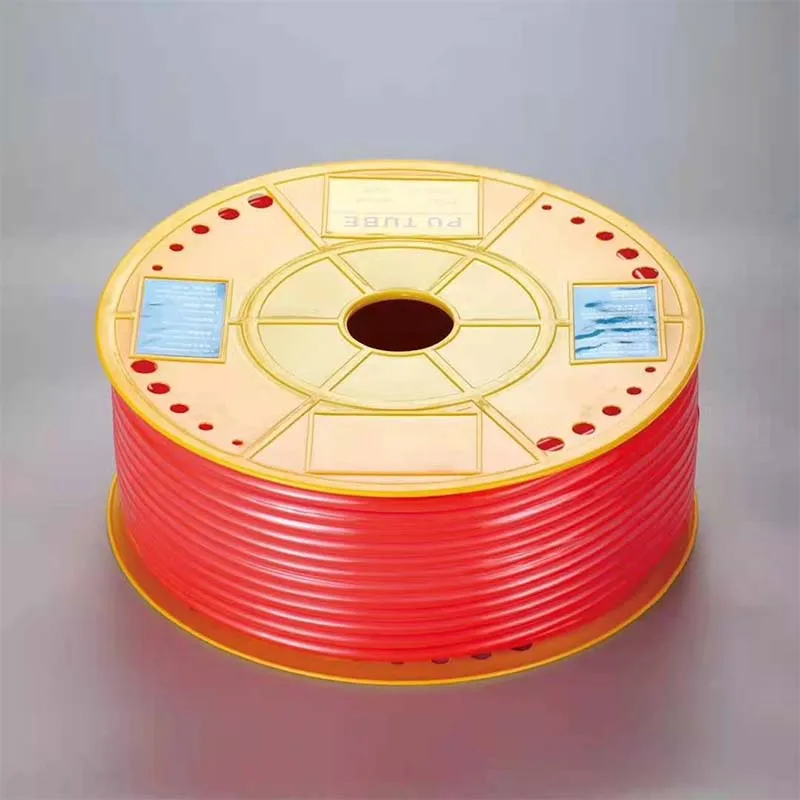
Diameter and length are also critical considerations when selecting an oxy-acetylene welding hose. The diameter should match the specifications of your welding setup for optimal gas flow. A hose that is too narrow may restrict gas flow, leading to inefficient burning, while a hose that is too wide may lead to waste and difficulty in handling. The length of the hose should offer flexibility and reach across your workspace without being cumbersome or creating a safety hazard.
Pressure capacity is another vital attribute. Oxy-acetylene hoses are available in different pressure ratings, typically classified by their working pressure and burst pressure. Ensure that the hose is rated well above the maximum pressure output of your gas cylinders to avoid the risk of rupture.
Compatibility with your welding equipment cannot be overstated. The hose must have fittings that match your welding torch and regulators. Universal connections can offer more flexibility in equipment compatibility, but ensure that all components are tightly secured to prevent leaks.
oxy acetylene welding hose
For the seasoned welder, maintaining an oxy-acetylene welding hose is a straightforward but essential task. Regular inspections are crucial. Inspect for any signs of wear, such as cracks, splits, or corrosion, which can compromise safety. Storing hoses in a cool, dark place away from sharp edges and chemicals can prolong their lifespan.
The use of color-coded hoses, often red for acetylene and green for oxygen, is a standard safety measure. This visual aid helps in quick and correct identification during setup and operation, reducing the risk of mistakenly cross-connecting the gases.
For welders concerned about environmental impact and safety regulations, selecting a hose that complies with industry standards and environmental legislation is important. Look for hoses that are certified and tested according to prevailing safety standards, such as ISO or ANSI.
From an authoritative standpoint, turning to reputable brands known for their quality and reliability is advisable. Brands with a long-standing presence in the welding industry usually have extensive research and development backing their products, leading to enhanced performance and safety. These manufacturers often provide detailed specifications and user guides, supporting best practices in various welding tasks.
As an expert decision, investing in the right oxy-acetylene welding hose translates to improved efficiency, reduced operational risks, and enhanced quality of welds. Whether you are an apprentice or a seasoned professional, understanding and prioritizing these crucial aspects in your welding toolkit will enable you to achieve exceptional, consistent results. Reliable resources and professional advice can further enrich your understanding, assuring trust and confidence in your welding endeavors.