For anyone involved in industries that require high-pressure systems, pneumatic tubing is an indispensable component. This component not only facilitates the transfer of pressurized air or gas but also plays a critical role in maintaining the efficiency and safety of pneumatic systems. Selecting the appropriate high-pressure pneumatic tubing is vital, ensuring resilience and performance in demanding environments.
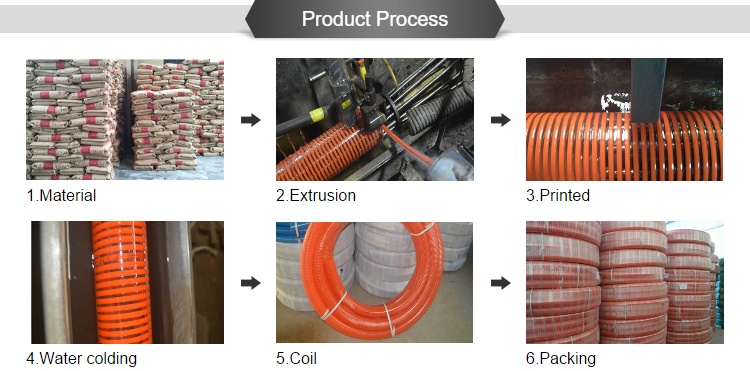
When considering high-pressure pneumatic tubing, it is essential to prioritize the material from which it's manufactured. Stainless steel, known for its robust properties and corrosion resistance, is a popular choice for heavy-duty applications. Its ability to withstand elevated pressures without deforming makes it an excellent selection for rigorous environments. In contrast, polyurethane tubing, offering remarkable flexibility and abrasion resistance, is suitable for applications where movement and adaptability are crucial. Each material offers unique benefits tailored to specific operational requirements.
Beyond material selection, understanding the correct sizing is essential for ensuring the proper function of pneumatic systems. Choosing a tubing diameter that balances airflow and pressure requirements can optimize system efficiency and prevent costly downtime due to pressure drops or system failures. Accurate measurement of both the internal and external diameters is crucial, as even small discrepancies can significantly impact performance.
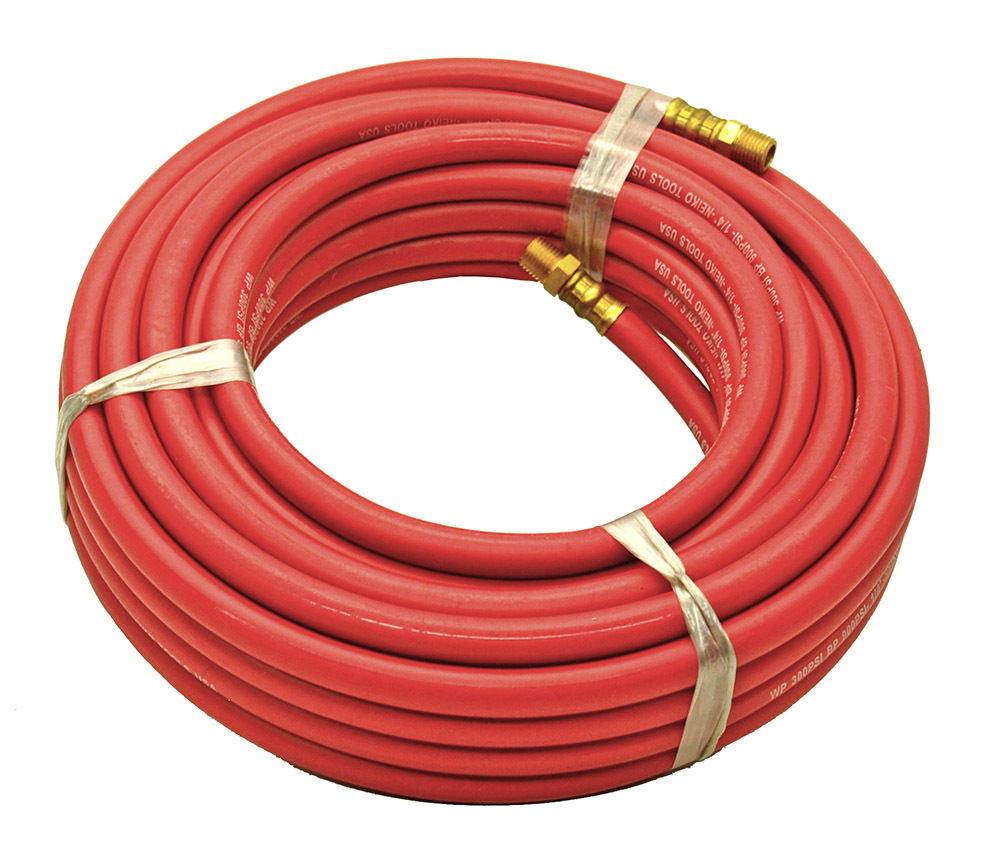
Furthermore, the environment in which the tubing will operate matters considerably. For instance, in settings with extreme temperatures or exposure to harsh chemicals, specialized tubing with additional coatings or treatments might be necessary. Data indicates that systems failing to account for environmental factors experience more frequent maintenance issues and tubing replacements, leading to increased operational costs.
High-pressure pneumatic tubing should also adhere to industry standards and certifications, ensuring quality and safety. ISO and SAE certifications, for example, provide assurances that the tubing meets internationally recognized benchmarks for performance and reliability. These certifications also communicate trustworthiness and authority, reassuring stakeholders and customers of the product's credibility and integrity.
high pressure pneumatic tubing
Installation and maintenance are other aspects not to be underestimated. Proper installation techniques, such as securing fittings and avoiding unnecessary bends or kinks, can prolong the lifespan of the tubing and enhance overall system performance. Regular maintenance checks, including inspections for wear, leaks, and pressure inconsistencies, are advisable to prevent unforeseen system failures.
Real-world implementations further underscore the importance of choosing the right high-pressure pneumatic tubing. In the automotive industry, for instance, air brake systems rely on high-quality pneumatic tubing to ensure safety and efficiency. Experience shows that selecting tubing specifically designed for high-pressure scenarios can significantly reduce the risk of brake failure, thereby enhancing vehicular safety.
Moreover, in the food and beverage industry, where pneumatic systems are often utilized for packaging processes, the selection of FDA-compliant tubing is crucial. This ensures not only the performance of the systems but also compliance with health and safety regulations. Expertise in selecting the appropriate tubing material and size can therefore make a substantial difference in operational productivity.
In conclusion, the strategic selection of high-pressure pneumatic tubing is paramount for industries reliant on pneumatic systems. By focusing on material, sizing, environmental conditions, and industry standards, businesses can ensure optimal performance and longevity of their systems. Proper installation and maintenance further contribute to system efficacy and safety, presenting a comprehensive approach to pneumatic system management. Investing in high-quality pneumatic tubing is not merely a matter of addressing current operational needs but also a forward-thinking strategy that aligns with industry best practices and fosters trust and reliability in high-pressure applications.