Flexible reinforced plastic hoses have gained significant traction in various industries, recognized for their versatility, durability, and adaptability. As an industrial component, their construction integrates the flexibility of plastic with the robust resilience of reinforcement materials, tailored to meet the high demands of modern applications.
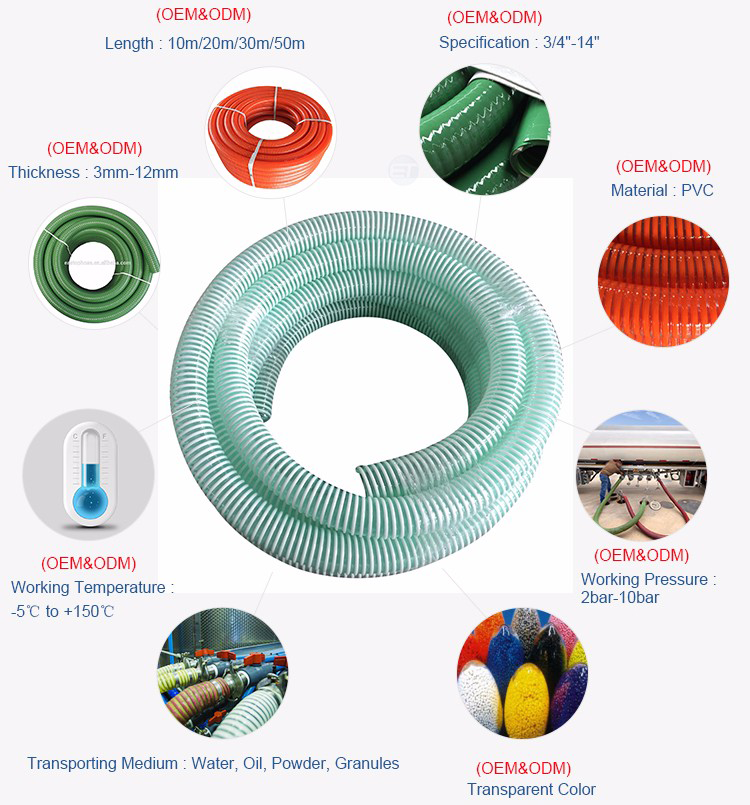
The journey of selecting the right flexible reinforced plastic hose starts with understanding its core components an inner tube, reinforcement layers, and an outer cover. The inner tube is typically crafted from materials like PVC, polyurethane, or nylon, each chosen for specific resistances or operational temperature ranges. The reinforcement, often a mesh or braided overlay of polyester, nylon, or even steel, enhances the hose’s pressure-handling capacity, offering unparalleled durability.
Industries such as agriculture, construction, and manufacturing benefit extensively from these hoses. In irrigation systems, for example, the hose's flexibility allows it to navigate complex routes, while its strength ensures long-lasting operation despite the constant flow of water. Construction sectors appreciate the hose's ability to transport cement, sand, and chemicals with minimal degradation, ensuring project efficiency and safety.
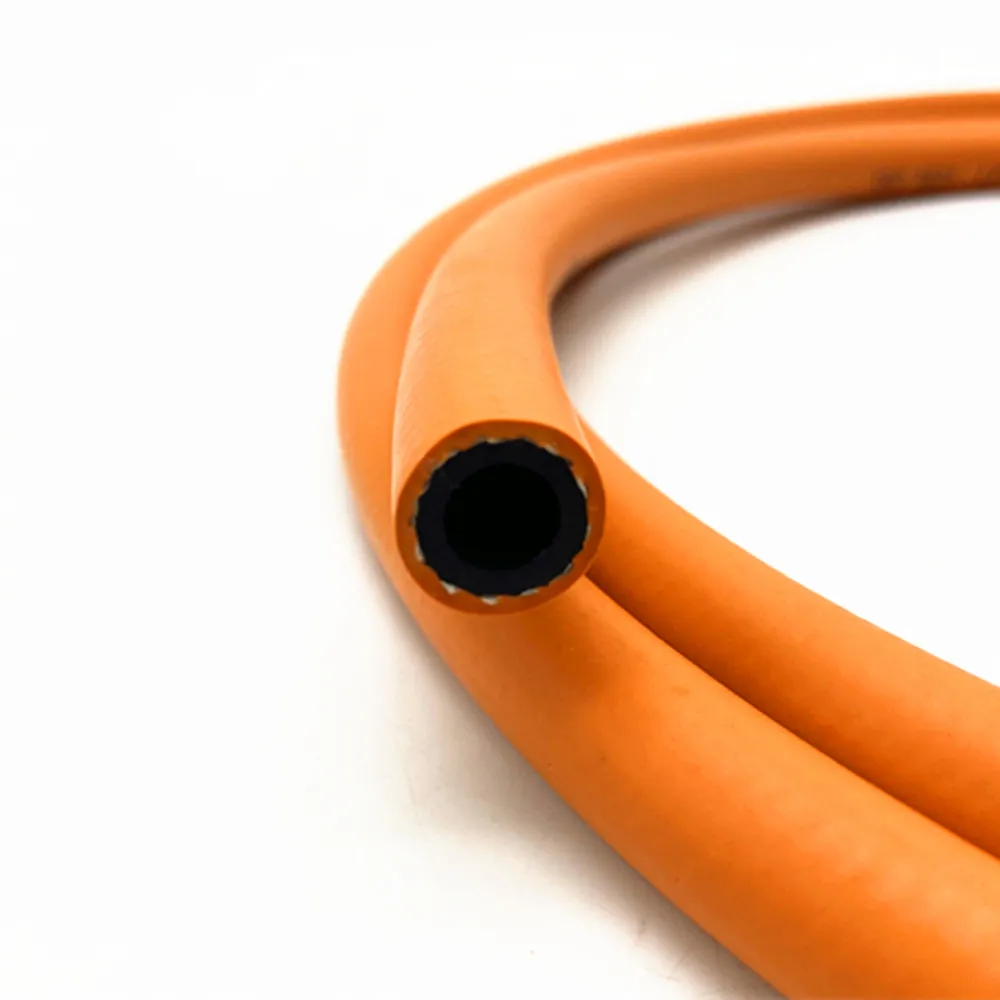
A critical aspect of flexible reinforced plastic hoses is their adaptability to various chemicals and environmental conditions. For instance, hoses used in chemical plants are designed to withstand corrosive substances, offering a non-reactive transport medium. This is crucial for maintaining the integrity of chemicals and ensuring safe operation within facilities.
Expertise in manufacturing these hoses involves a deep understanding of material science and engineering. The production process is a meticulous blend of selecting appropriate material combinations and employing advanced manufacturing techniques. Precision in the reinforcement pattern is crucial as it dictates the hose's performance characteristics, affecting everything from flexibility to tensile strength.
flexible reinforced plastic hose
Another compelling attribute is the hose’s longevity. The outer layer is often embedded with UV-resistant materials, preventing degradation under constant sunlight, a common concern for hoses employed outdoors. Moreover, many are formulated with advanced polymers that resist wear and tear, making them a cost-effective solution in the long run.
Authoritative voices in engineering and material science endorse flexible reinforced plastic hoses for their safety and reliability. Rigorous testing protocols ensure each hose meets industry standards, including burst pressure, tensile strength, and flexibility assessments. Their compliance with these standards acts as a testament to their quality, fostering trust among end-users who seek reliability in high-stakes environments.
In terms of trustworthiness, the traceability of materials used in these hoses is crucial. Reputable manufacturers provide transparent records of material sources, reinforcing their commitment to quality and ethical production practices. This transparency is particularly vital in sectors like food and pharmaceuticals, where hose integrity directly impacts product safety.
Real-world applications underscore the hose’s capacity to improve operational efficacy. For instance, in dairy farming, flexible reinforced plastic hoses facilitate the hygienic transport of milk, safeguarding against contamination and ensuring freshness. Their ease of cleaning further enhances their appeal in environments where sanitation is paramount.
In summation, flexible reinforced plastic hoses represent a confluence of innovative engineering and practical application, serving as vital components across various industries. Their construction, adaptability, and durability are supported by expert manufacturing processes and authoritative endorsements. These attributes make them not just a choice, but an invaluable asset in sectors demanding efficiency and reliability. Investing in such precision-engineered products translates into operational longevity, enhanced safety, and cost savings, underscoring their indispensability in progressive industrial settings.